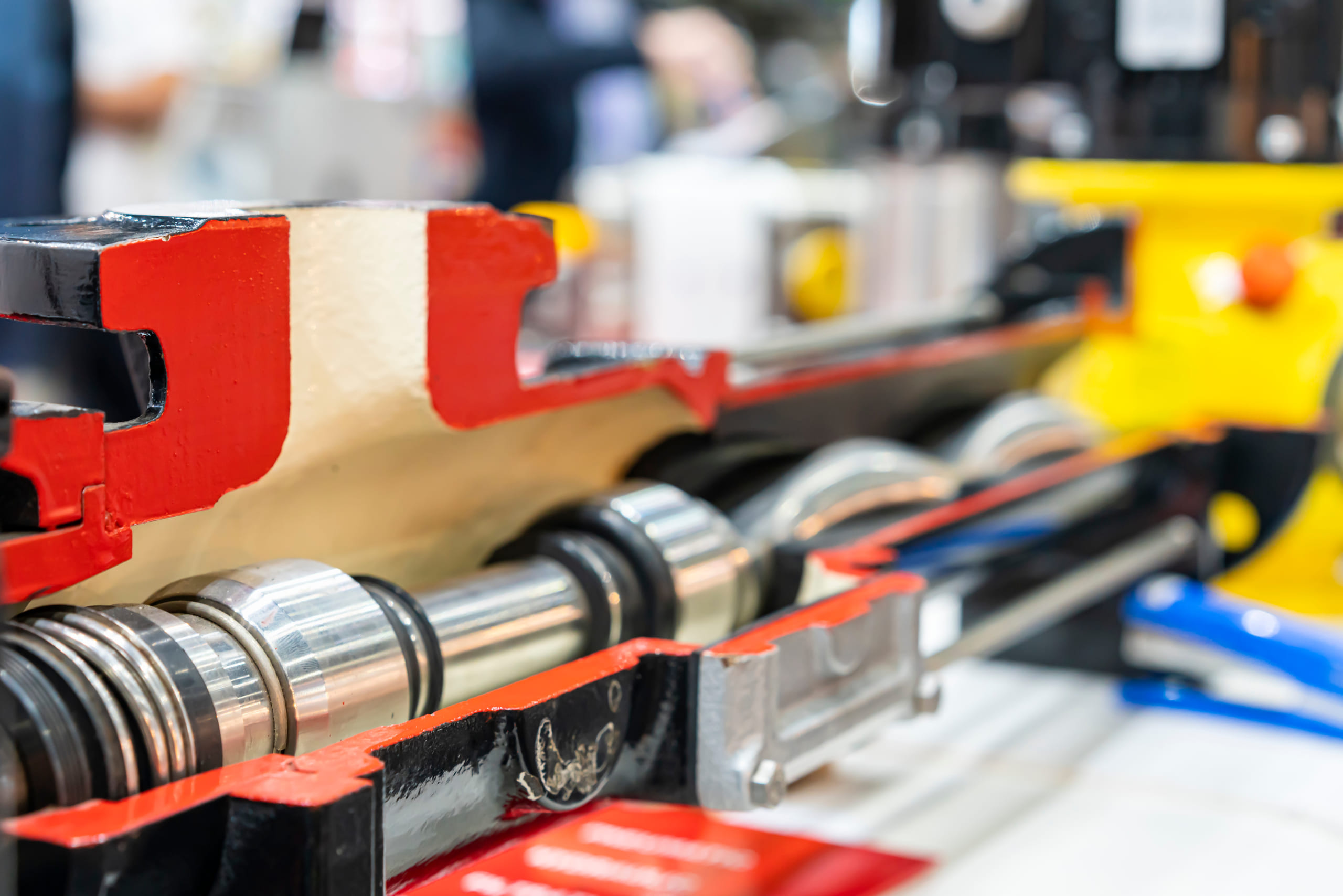
Last updated: August 30, 2024
Key Takeaways
- Overview of the Progressive Cavity Pump: This paper highlights the mechanics of progressive cavity pumps and their suitability to precise conveyance of viscous fluids and fluid-like substances.
- A Versatile and Adaptable Design with a Century of Industry Wisdom: It covers the variety of needs and conditions that PCPs can be built to meet, and highlights how manufacturers have refined and iterated on the concept since its invention.
- Value as a Transitional Tool: The paper addresses how this technology’s suitability to both waning industries such as fossil fuels and emerging industries such as clean energy adds value to both the products themselves and to enduring partnerships with manufacturers.
- Unrealized Potential for Future Industries: It outlines how the digital era simultaneously drives demand for high-precision conveyance solutions, while also creating the tools to better utilize and facilitate the precision and control they offer to minimize waste and maximize efficiency.
Progressive Cavity Pump
In 1930, French engineer René Moineau developed a new type of compressor for jet engines, which became the basis for a pump design that has been utilized and iterated upon throughout the near century since. The unique operating principle of what is now known as the progressive cavity pump relies on a spiral-shaped rotor-stator pair in which the spaces between the rotor and stator form a series of discrete cavities that move as the rotor turns while maintaining steady shapes.
The PCP is characterized by its ability to pump low to medium volumes of viscous fluids with minimal shear at a near-perfectly steady rate with a high degree of efficiency and control. Because of these benefits, this type of pump has seen regular usage in certain industries, such as chemical slurry pumping and the dispensing of foods and cosmetics.
However, new demands in the modern era, especially the global push for cleaner energy, are driving the emergence and expansion of numerous industries such as the battery production and chemical waste management industries, the needs of which the progressive cavity pump is well-suited to meet. This rapid change in the global manufacturing sector represents a golden opportunity for PCP manufacturers to not only expand into these growing industries, but also to capitalize on greater visibility, publicity, and awareness among industry professionals to reach out to other established industries as well.
The PCP companies in the best position to capitalize on the rising awareness and prominence of this type of pump within the manufacturing sector will be those that have already developed a wide array of PCPs and supporting accessories for various specialized applications. These companies and their partners are poised to market their products to existing businesses and emerging technological fields to spearhead a golden age for the PCP industry.
Mechanics and Benefits of the Progressive Cavity Pump
The operating principle of the progressive cavity pump is fundamentally very simple and can be scaled up or down and iterated upon in a variety of ways to meet different demands. While they are not suited to large-scale, high-volume pumping of heavy and crude substances, the main draws of PCPs derive from their low shear and high control.
The cavities in a PCP maintain a constant shape as they move along the length of the stator, and this allows the contents of each cavity to be conveyed with minimal shear. This is especially invaluable to the conveyance of highly viscous fluids, as well as abrasive mineral slurries, for which friction tends to increase the energy demand and reduce the life cycle of the operating pump. Conversely, this also allows PCPs to pump many delicate substances such as food products or cell cultures while causing minimal damage.
Most pumps that separate their conveyed contents into discretized quantities, e.g. gear, lobe, or rotary vane pumps, suffer from a slight oscillation in their flow rate and this can make the resulting flow choppy and limit the precision with which dosages can be controlled. The progressive cavity pump’s design bypasses this pitfall, as each cavity’s tapering is matched exactly by the next cavity’s widening, maintaining a near-perfectly constant total cross-sectional area. This allows PCPs to operate with a very high degree of control, maintaining a steady flow rate directly proportional to the rotational velocity of the rotor, which can be adjusted or reversed with remarkable precision while being highly resistant to unwanted backflow.
Because these pumps can be programmed and fine-tuned to steadily dispense precise quantities and are resistant to jamming caused by friction or shear, they can produce identical outputs with a high degree of consistency. This makes them highly compatible with automation, and as an increasing number of industries task machines with an increasing amount of work while minimizing human input, the value of this precision and consistency will continue to grow and potentiate further demand for PCP technology.
Suitability to Growing and Emerging Industries
While PCPs currently see usage in oil and coal slurry pumping, the technology is highly robust and adaptable, and has the potential to retain or even grow in popularity and usage as the global economy transitions away from fossil fuels. The growing demand for clean energy and reduced pollution is driving industries which also have the potential to make great use of progressive cavity pumps, as numerous emerging manufacturing sectors require substantial mineral inputs and generate considerable viscous waste outputs. Many of these processes are chemical in nature and dependent on precisely managed ratios to produce optimal results, while more broadly, the ability to output a consistent dosage can help to minimize waste and redundancy.
Arguably the most prominent and high-profile of these rising sectors is the battery industry; as countries transition a larger percentage of their power grids to clean energy sources such as wind and solar and our transportation shifts toward electric vehicles, this will necessitate storage solutions. These industries are heavily dependent on lithium-ion slurries, which the progressive cavity pump is distinctly adept at dispensing safely and efficiently. Furthermore, the battery industry has the potential to become economically and environmentally sustainable due to the rising material and economic viability of battery recycling, which will require further infrastructure that PCPs have the potential to be a part of.
Manufacturing waste management is another growing field in which, if they are not already being used, PCPs have the potential to carve themselves a lasting niche. From the simple removal of inert byproducts to the secondary processing of waste via chemical scrubbers to ensure that its toxicity and environmental impact are within regulation, an increasing number of manufacturers are investing in technologies outside the direct production of goods to meet corporate, national, and global environmental goals. Any manufacturer that processes large amounts of viscous or abrasive waste may find PCPs beneficial to their overall efficiency, as they are highly effective at transporting the waste from individual devices into a larger piping system that can be driven by a different type of pump.
Progressive cavity pumps are currently used in many industries that deal in consumable products such as food, cleaning solutions, and cosmetics, but they are not ubiquitous in these industries and, as with any tool, some companies do not incorporate a beneficial device into their business model simply due to poor awareness. The benefits of numerous high-profile use cases, especially coupled with the positive optics of environmentally conscious business and manufacturing, present a golden opportunity to bolster the marketing and support for progressive cavity pumps to a wider range of potential customers.
The Value of Industry Wisdom
The principal benefits of the progressive cavity pump are achieved through the interaction between two large mechanical components, a rotor and a stator, and this makes most PCPs relatively easy to assemble and disassemble for cleaning and maintenance due to the relative lack of smaller, more intricately arranged components. The tradeoff in this design is that both the rotor and the stator are expensive and materially demanding to replace, and their intricate shapes are susceptible to failure after a moderate amount of wear.
Because the operating principle of the PCP has remained virtually unchanged since its invention, smaller or less specialized manufacturers will often limit their product lines to a small handful of models with little variation aside from scale and power. However, the progressive cavity pump is not a one-size-fits-all tool, and emerging industries would benefit greatly from the generations of industry wisdom accrued by specialized PCP companies who have paradoxically achieved far greater versatility.
Broadly speaking, a progressive cavity pump can convey any fluid or fluid-like substance so long as it is powered by a motor with an appropriate range of outputs and its cavities are of a size suited to accommodate the substance in question. In practice, without greater specialization to their designated task, without other types of pumps operating in tandem, and without experts available to provide their support and recommendations, PCPs can become cumbersome to incorporate and maintain while not operating at the efficiency they promise.
As progressive cavity pumps rise in demand and gain greater visibility across a multitude of industries for reasons outlined in the previous section, misconceptions and even outright misinformation will be inevitable and many new buyers will be susceptible to purchasing inferior and counterfeit products. A layperson, even a trained engineer unfamiliar with PCPs, cannot be expected to know which materials conveyed at which flowrates will necessitate more durable rotors and stators, or which applications and fluids will require longer pumps with more cavities to protect against counterpressure, and may find themselves needing to replace lower quality parts at inordinate frequencies or purchasing upsells not necessary to their intended output.
Consequently, companies with deeper knowledge of the intricacies of progressive cavity pumps will be greatly valued. The most successful PCP manufacturers will likely be the ones that utilize their familiarity with the intricacies of these tools and their applications to not only develop wider ranges of products finely tuned to specific types of materials and factory setting, but to design supporting hardware and software to facilitate the operation of their pumps in tandem with other relevant machinery.
This approach can be further bolstered by developing close relationships with other companies that specialize in complementary tools and supplies, ranging from robots to valves to lubricants. Some veteran companies, such as Heishin in Japan and Netzsch in Germany, have already taken some or all of these leaps, positioning themselves as potential leaders in an industry primed to enter a period of rapid growth. These attributes should be sought after not only for the quality of their products, but to reap the benefits of their experience in integrating their pumps seamlessly into a variety of factory conditions and workflows.
Conclusion
While the technology of the progressive cavity pump has existed in some form for nearly one hundred years, the high precision made theoretically possible by their design could not be fully realized until the digital era allowed us to control their output time on a scale of milliseconds. The use of electronic controllers to more efficiently regulate these tools in the workplace has opened the door to synchronizing their flows with the movements of robots and other moving parts, coordinating multiple pumps to create mixtures by dispensing precise ratios, and many other applications only made possible over the last three decades.
In spite of these innovations, the synergy between PCPs and adjacent technologies has arguably not yet been perfected. For example, while a robot can be programmed to dispense adhesive as it moves along a linear path, human experience accumulated through trial and error is still broadly necessary to match the flowrate to the fluid properties, robot movement speed, and desired layer thickness, a process that has the potential to be made more user-friendly with some improvements to the software that facilitates communication between these machines. Careful tolerancing is also needed to position the nozzle of a dispenser at the ideal distance from the target surface, though some laser distance measurement tools are being developed to automate this process.
Other ways the industry can continue to grow and improve range from the development and use of more cost-effective materials that do not compromise durability, to the modification of the pumps’ external hardware to better specialize for specific applications. Pumps have been specialized to draw from hoppers or drums instead of pipes or tubes, to prioritize durability or to gently dispense delicate substances, to be easily transportable or to be fixed in place.
As existing industries grow and new modes of manufacturing we cannot currently imagine continue to emerge, even the most robust technologies are only as versatile as their makers are adaptable to these changes. At the time of writing, the Progressive Cavity Pump market is projected to grow by approximately $800 million in the next five years, but for that growth to bring meaningful improvements to industries, workers, and society, it must be driven by more than a passing fad. PCP manufacturers will bear a responsibility to meet the needs of the changing world and spread awareness of their technology, and industries will be equally responsible for adopting these tools based on properly informed decisions rather than hype. If all parties rise to meet these challenges, then trusting partnerships can be established, upon which a sustainable, mutually beneficial future can be achieved.