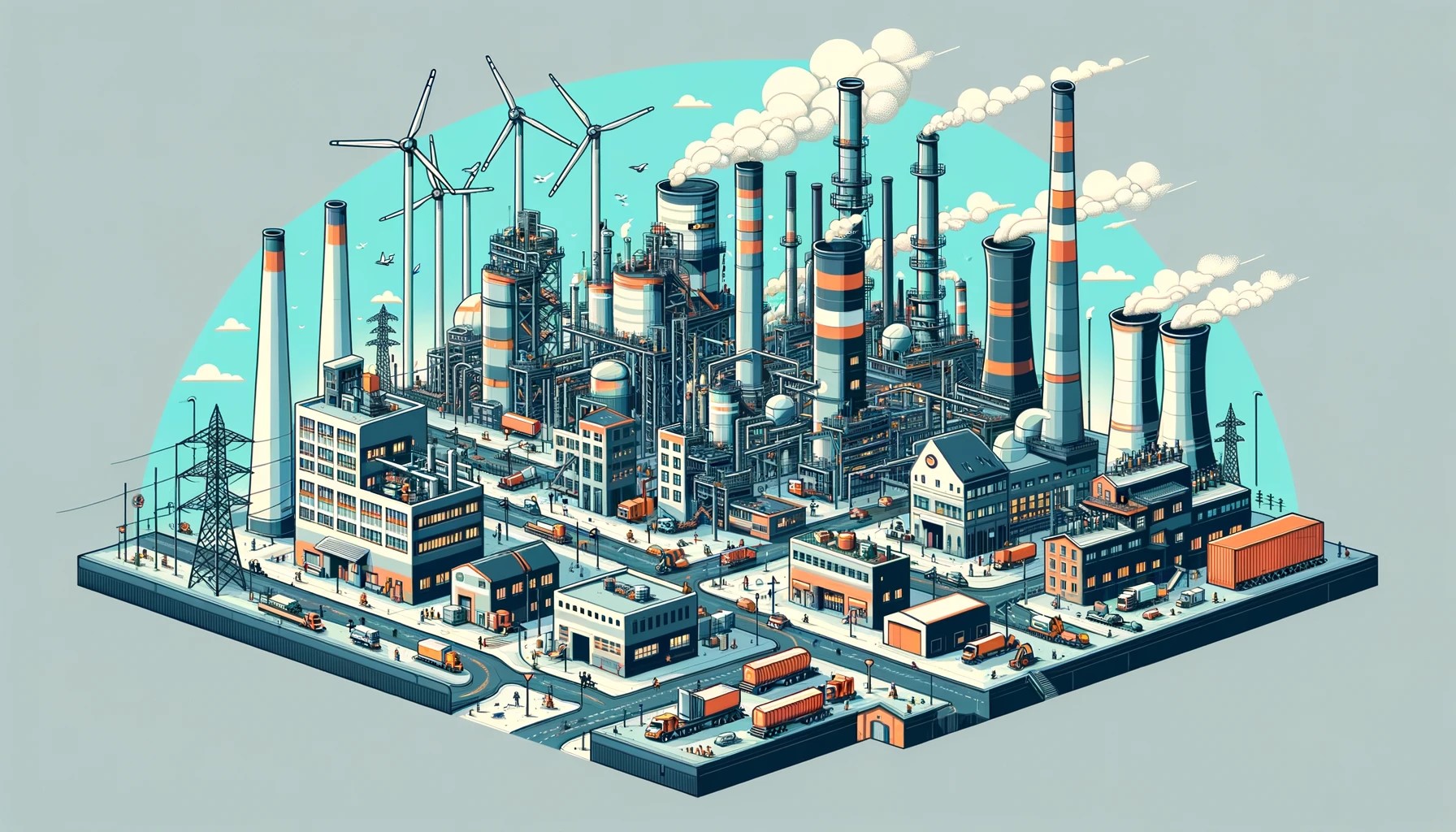
Last updated: February 21, 2024
Key Takeaways
- Challenges with Wired Testing: Current wired testing methods are limited by accessibility, safety risks, and scalability issues in complex machinery.
- Benefits of Wireless Technology: Wireless instruments offer a solution, improving safety, ease of use, and efficiency in data collection, especially in large-scale operations.
- Positive Workplace Impact: Implementing wireless testing can significantly improve the testing process, reducing downtime and enhancing workplace efficiency.
A Framework of Incorporating Wireless Measurements and Data Collection
In 2020 GE Digital published their findings that over a period of three years, approximately five of every six (82%) manufacturing organizations self-reported experiencing unplanned downtime, costing an estimated average of $22,000 per minute of inactivity.
Additionally, 90% of respondents acknowledged that their companies’ preventative testing practices were insufficient, suggesting that many failures leading to unplanned downtime have been preventable, and further indicating that without improved preemptive measures these failures will continue to occur.
However, modern manufacturing is increasingly characterized by complex systems of interconnected parts and processes with numerous emergent properties and points of failure. Consequently, when testing for failure conditions such as electric current or thermal and mechanical strain, modern test engineers and technicians are often required to navigate heavy machinery and a variety of potential hazards. Furthermore, many test technicians are faced with the challenges of gathering data from devices that cover wide and complex ranges of motion or operate in enclosed spaces, and when working with larger and more intricate machinery with greater numbers of points of failure, these obstacles are proportionally amplified.
Although regular prognostic testing is unquestionably beneficial to any manufacturing operation in the long-term, many businesses have found or inevitably will find the path to incorporating these processes fraught with challenges of accessibility, scale, and safety. No matter a company’s culture or corporate philosophy, if a task’s benefit is not necessary and apparent in the short-term, sufficient inconvenience becomes a significant deterrent to its introduction and consistent execution, as even well-meaning employees can be incentivized to cut corners to meet their company’s immediate goals.
Conversely, then, the benefits of tools that increase the efficiency and convenience of these preventative tests can extend far beyond a linear decrease in time spent on the tests themselves. Indeed, if a high upfront demand for training and time allocation is a deterrent to implementing a change on paper, and a significant time cost compels employees to rush through the process in practice, then an increase in convenience can change how these tests are perceived and executed at all levels.
Considering that manufacturing is an expansive field with wildly varying needs across different companies and sites, no one issue on this front can be considered universally load-bearing, and no single improvement should be treated as a panacea. This paper focuses specifically on the inconveniences of wired measuring instruments and the practical advantages of wireless instruments that have the potential to significantly mitigate challenges of accessibility, safety, and scale, while also acknowledging the potential pitfalls of careless implementation.
The purpose of this analysis is to outline a framework to help businesses evaluate the net benefits of incorporating wireless measurements and data collection, specifically as tools for greatly increasing the ease and efficiency with which preventative testing can be safely carried out, thereby changing how these tests are perceived by employees and the culture surrounding them.
Challenges: Accessibility, Scale, and Safety
1. Accessibility
For the purpose of this paper, the term “accessibility” encompasses the ease with which a person can reach the target area of a machine or production line in order to apply the appropriate measuring instrument, as well as the number and complexity of steps required to transmit and collect the measured data. When using an instrument that depends on cable connections to convey its readings, technicians are required to not only directly access the point being measured, but also to navigate a complete route for the cable connecting the instrument to its receiving device, all of which demonstrably add to the time cost of testing.
Properties such as strain, temperature, and voltage may need to be measured during machine operations to yield the data necessary for an informed prognosis, and this requirement has the potential to introduce a host of obstacles that hamper the use of wired instruments. Firstly, the entire length of the instrument’s connection to its receiver needs to be accounted for to ensure that it does not cross the range of motion of any moving parts. In a sufficiently complex production line, this necessitates careful planning and attention to detail, often resulting in the wires taking long and circuitous paths.
Additionally, if the part being measured is itself subject to a wide range of motion, then the wiring will need to accommodate every state of that path. A long path of movement will at times result in slack in the connecting wire, which if not carefully sequestered can become a liability, which will be discussed further in the Safety section.
These challenges are compounded when the target component’s path of movement includes a tight or enclosed space, or when they incorporate rotational motion, and these are circumstances under which the benefits of bypassing the need for a continuous wired connection are made especially apparent.
Furthermore, the tangible human benefit of reducing the physical demands of installing a measurement device on the tester should not be overlooked, nor should the capacity to log larger amounts of data with less travel between data collection points in larger facilities. Greater accessibility not only increases the number of employees capable of performing a task, but also reduces the time and energy cost a task place on any employee.
2. Scale
An emergent obstacle to preventatively testing or troubleshooting large and complex production lines is that their size can slow the process of gathering and compiling data across multiple points of failure. The setup necessary to collect simultaneous data across physically distant locations may risk becoming ponderous and materially demanding, requiring either multiple data collection devices operating separately, or an elaborate setup to simultaneously connect all measuring devices to a single receptacle.
Conversely, attempting to measure a line’s points of failure one-by-one has the potential to greatly increase the line’s downtime, especially when running tests that require temporarily running the line sub-optimally, or when using measuring devices that could be more efficiently installed and uninstalled simultaneously rather than sequentially.
As outlined in the previous section, each wired measuring device becomes a potential obstacle to all other devices occupying scarce physical space, an issue that compounds as the number of measured data points increases. This challenge of accessibility dovetails to become a bottleneck for testing efficiency, as the chief obstacle to efficient, necessitating sequential rather than simultaneous tests that lead to more time spent either running the machinery in a testing state or reposition the testing devices at different points of failure.
Such a reduction of redundancy is especially valuable when testing machines that take time to safely power down due to hazards such as high temperatures or toxic fluids that need to be purged. Additionally, eschewing manual data entry not only saves time, but removes the risk of human error due to misread or incorrectly entered figures.
Wireless data logging greatly increases the ease and efficiency of simultaneous collection from multiple data points due to the reduced space they occupy, while also potentially simplifying the data compilation process due to the shared temporal context of the data gathered at each location and the greater ease of transmitting all collected data to a single device capable of performing analysis without the risk of human error inherent to manual data entry.
3. Safety
Safety becomes an additional concern when gathering data from a production line that contains hazards such as live electricity, heavy machinery, or extreme temperatures. Workplace injuries, in addition to the harm they cause to the employee, also result in unplanned downtime, loss of productive personnel, possible damage to the company’s reputation, and a myriad of other costs both financially and morally.
Even in a statistically safe workplace operated by well-trained and highly disciplined personnel, any opportunity to obtain identical data while reducing the frequency and complexity of direct human interaction with hazardous conditions is effectively an increase in overall workplace safety; the Efficiency section has addressed how wireless instruments can help achieve this goal.
It should be noted that even when a human being is not immediately present, a misplaced tool or a cable that inadvertently passes through a machine’s range of motion risks damaging the tool in question as well as the surrounding area; the potential for wireless instruments to mitigate this hazard has been outlined in the Accessibility section.
Furthermore, while not as dramatic, wireless measurement data collection offers the simple convenience of being able to carry a computer or other data receiver around a workspace without worrying about the limited length of a wired connection, and to move a greater distance from the measured areas without concern that the connecting cords may become a workplace tripping hazard. Tripping over or otherwise tugging a cord not only risks an employee suffering from a fall, but also has the potential to pull on any machinery the cord is attached to or routed through.
Potential Pitfalls of Wireless Measurement Data Collection
While offering many conveniences, wireless measurement data collection comes with some unique limitations and should not be carelessly implemented as a replacement for wired data collection in every circumstance.
First and foremost, while wireless measuring instruments dispense with the need for a continuous connection from the immediate measured area to an outside data receptacle, the necessary power storage and transmission hardware take up physical space that must be accounted for, as a place near an area to be measured must be identified to accommodate this hardware’s bulk. This tradeoff must be considered when applied to sensitive opponents for which the resulting weight imbalance may disrupt their functionality, or for components that pass through narrow spaces. Even when they are not a prohibitive obstacle, the physical weight, size, and positioning of the transmission component should always be carefully considered when applying these measuring devices to a system, as should its suitability to its environment.
Furthermore, their reliance on internal batteries effectively means that wireless measurement devices cannot be installed permanently in machines that require constant monitoring. Limited battery life restricts these tools to periods of continuous usage that can be measured in hours or days rather than weeks or months. Permanent installation of a wireless measurement device should be avoided unless a device requires constant monitoring while being completely incompatible with wired data transmission.
The specific vulnerabilities of the batteries and transmission hardware, such as to heat, moisture, and electromagnetic interference, must also be accounted for; protective casing can be used to mitigate these hazards, but prolonged exposure to conditions such as extreme heat can still impair and permanently damage these devices, especially in enclosed spaces.
On a whole, while wireless measurement devices are very useful tools that address many workplace inefficiencies and hazards that occur when using wired instruments, they have their own unique physical and technical restrictions that testers must learn to mindfully work within and around. Furthermore, these instruments are not suited to long-term integration into machines that require constant monitoring, and their usage is best restricted to temporary and periodic applications, for which they are overall well-suited.
Short-Term Convenience, Long-Term Confidence
While no new tool is without a learning curve, the introduction of wireless measuring instruments to a workplace can substantially ameliorate the inconveniences of regular preventative testing and reduce employee exposure to regular hazards, and these benefits scale well to larger production lines with increasing numbers of points of failure.
Significant time cost and inconvenience, especially in a highly competitive work environment, can incentivize cut corners, and these issues have the potential to lead to essential tests being performed either less frequently or less safely. The introduction of user-friendly tools to ease the testing process not only reduces the planned downtime spent on each round of testing, but also changes how the testing process is perceived and increases the likelihood that it will be done well and diligently.
Insufficient preventative testing, one of the leading causes of unplanned downtime and financial loss in the manufacturing sector, is a multi-faceted issue that no one solution can eliminate in totality. This also means that many companies have numerous opportunities to increase their profits with every step taken to remove obstacles to consistent and effective testing. Improved testing tools that enable more efficient procurement of data are one such step, and one that addresses the human root of the issue without devaluing the people whose daily contributions keep these industries running.
This paper has illustrated numerous avenues by which wireless instruments can reduce the time and inconvenience of testing, which carries tantalizing benefits to businesspeople and managers who have delayed the implementation of new testing protocol while reducing the burden testing places on the employees who operate the machinery. Even for companies with dependable testing protocols in place, reducing planned downtime should still be a desirable outcome, and for those continuing to suffer from sporadic unplanned downtime, the benefits of reducing the frequency of such incidents are not abstract, they are measurable.
For questions, email us at resources@n-denkeiamericas.com.