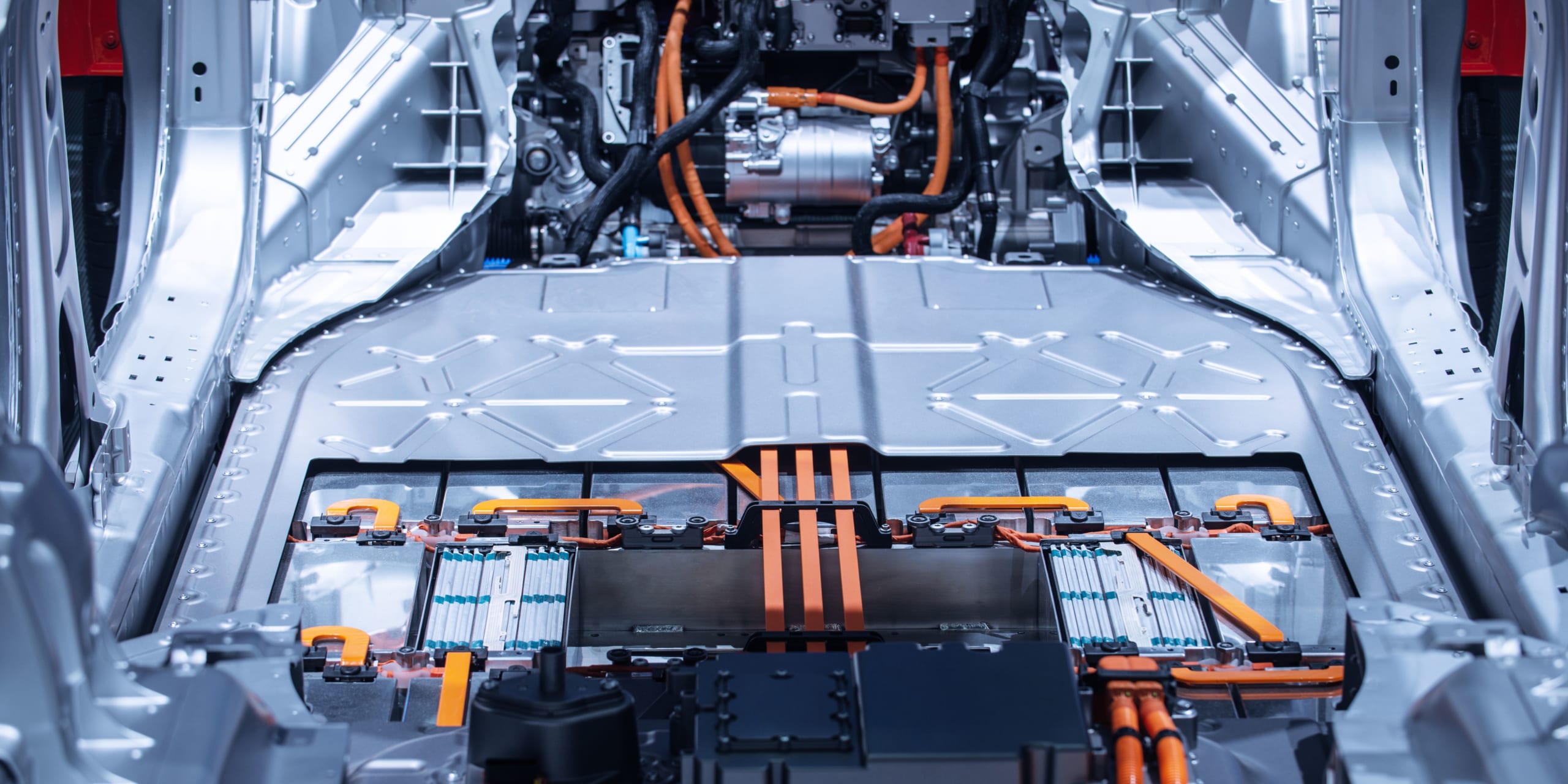
Last updated: March 29, 2024
Key Takeaways
- Emerging Importance of Serialized Visual Data: The paper highlights the growing reliance of the automotive and robotics industries on cameras and the critical role of serialized visual data in enhancing machine performance and safety.
- Design Challenges and Solutions: It addresses the design challenges posed by traditional bulky camera cables in complex machines, and how data serialization offers a space-efficient and reliable solution.
- Benefits of Serialized Data Transmission: The paper outlines the advantages of using serialized data, such as improved maneuverability, increased sensor capacity, and enhanced safety through redundancy.
- Balanced Approach to Technology Implementation: The paper advocates for a thoughtful, application-specific adoption of data serialization, recognizing its benefits while being mindful of its limitations and tradeoffs.
Serialized Visual Data in Automobiles and Robotics
The automotive and robotics industries are becoming increasingly reliant on cameras, either as safety features to protect against human error, or as tools to navigate their environments autonomously. When designing the machines to utilize cameras and make use of the visual data they provide, a steady and dependable connection with negligible lag is highly desirable, and often an outright necessity where safety is concerned. To that end, integrated cameras generally require large connector cables to transmit their data seamlessly to the central processing units of the machines processing them, and this physical bulk can be a significant source of design tension.
A large and complex machine, such as an automobile, will often utilize multiple cameras and tend to position them at extremities far from the CPU, where they can be most useful. Consequently, this necessitates a greater length of connecting cable, which is more likely to need to pass through bottlenecks in the surrounding structures, competing for space with other connections that manage various controls and communications. For larger cables, suitability to their connecting route must be considered, as thicker cables not only take up more space, but also cannot bend as sharply.
In order to transmit visual data with close to zero delay, most cameras used in automobiles and robots currently depend on wide and bulky compound connectors such as ribbon cables, which suffer from all of the aforementioned design tensions. Thicker cables are also more likely to be subjected to pinching and compression, turning them into large potential points of failure. As increasingly powerful computers and ambitious vehicle and robot designs push us toward the incorporation of greater numbers of cameras and other sensors, the space needed to connect everything to the CPU becomes increasingly valuable, and new methods of data transmission will be needed to accommodate the ensuing density of information without compromising consistent, dependable flow.
For the foreseeable future, wireless connections are not suited to the task, as they cannot be relied upon for sustained and consistent transmission of detailed visual data without significant loss or lag. A more immediately feasible approach that utilizes existing technology is to change how the data is transmitted so that it can pass through narrower connections without compromising speed, efficiency, or resolution. This can be approached through data serialization, which converts a camera’s output from a series of parallel elements that traditionally require a bulky compound cable to a single data sequence in a set pattern that can be conveyed along a much smaller single cable. This data can then be deserialized via specialized hardware into a usable form to be interpreted by the central computer.
Integration with Testing Infrastructure
Having outlined some of the benefits of video data serialization and the potential to strengthen and improve upon existing designs, it bears mentioning that most testing infrastructure for vehicle and robot development is not designed with this form of data transmission in mind. With vehicles especially, given the human safety concerns inherent to these creations, simulations are typically used to test a computer’s response time and intelligence long before field testing can begin, requiring video data to be transmitted in a form the CPU is prepared to receive and interpret. Thus, adapting a test apparatus to output serialized video data presents a design challenge, especially for machines that require tight, precise reaction times that must also be verified during testing.
Like deserialization at the end of the transmission process, converting video data to a serialized form to transmit to the CPU requires specialized serialization hardware. For machines such as electric vehicles that depend on their cameras for navigation and safety, simulation videos used for testing cannot be serialized in advance, but need to be played, serialized, transmitted, and then deserialized in real time. This is because these machines’ central computers are not equipped to play video files, they are designed to respond to their environments frame-by-frame. Serialization hardware is not always necessary in a machine’s final design when using cameras that can directly output serialized signals, but a serializer board is essential to the testing process and can be easily and seamlessly integrated into most existing test apparatuses at negligible cost to transmission time.
Serializer boards also carry the mundane yet significant benefit of allowing testing to occur more easily, as an external camera is often simply an easier access point that requires less disruption to the surrounding machinery compared to a CPU. This is beneficial not only during testing at different stages of assembly, but also during diagnostic troubleshooting for machines that have been fully assembled and operational, or when verifying the success of a software update. Furthermore, some pre-existing testing infrastructure is already designed to connect at the camera end, so the availability of serializer boards averts the need for what would otherwise be a significant overhaul in their process and apparatus.
Data Serialization is not a Universal Solution
In an increasingly automated and digital era, the incorporation of serialized camera data has the potential to facilitate innovative designs that would otherwise be in tension with, if not precluded entirely by, the physical limitations of cameras and the cables needed to connect them. That said, serialization is not a universal solution and should not be carelessly integrated in all circumstances. Every new technology comes with drawbacks and tradeoffs, and it would be irresponsible engineering to recklessly encourage blindly buying into every exciting new innovation for the sake of innovation.
First and foremost, it bears repeating that a deserializer board is a physical object in its own right, and needs to be housed somewhere unobtrusive. In smaller machines where the camera is either positioned very close to the processing unit, or where the path between the camera and the CPU are unobstructed and a larger cable is not particularly inconvenient, the bulk of a deserializer board may not be worth the tradeoff. Data serialization is specifically a solution to the inconvenience of compound cables, and should be treated as such; they offer little benefit to designs in which larger cables are not a significant source of tension.
Another notable design concern is that, while the smaller cables used to transmit serialized camera data have reduced collision and greater resistance to bending and twisting fatigue, their small size makes them delicate, and they are still vulnerable to external damage from force, friction, and heat. In some specific high-risk areas, additional padding or insulation may be necessary to protect these cables from their surroundings. This will not necessarily negate the benefits of using smaller cables, since dangerous areas are not guaranteed to overlap with physical bottlenecks, but it is a concern nonetheless and should always be taken into consideration.
And finally, one of the chief reasons for implementing serialized data is to preserve the benefits of physical data transmission: speed, steadiness, and reliability. In slower moving machinery where precise, consistent reaction time is not as much of a concern, a slower frame rate may be acceptable, and the machine can safely stop the moment it loses its visual connection, a wireless connection may be just as suitable a solution, if not better. This is not recommended for fast-moving machines like cars, but it might turn out to be preferable for certain applications in the field of robotics.
Facilitating New Frontiers in Design
As robots and vehicles are outfitted with increasingly powerful and efficient central computers with more sophisticated A.I., the physical demands of cameras and other sensors becomes the greatest obstacle against fully capitalizing on the potential of that computational power. Serialized data transmission is a tool that can easily be introduced to many existing designs to remove the need for broad and cumbersome compound cables and widen any bottlenecks these cables previously caused, thereby helping to fully realize that potential.
No matter how powerful and intelligent a computer may be, it can only ever know as much about its surroundings as it is given by the sensors connected to it. Smaller connector cables are one way to enable a greater number of sensors to be connected to a single processor, and a greater number of sensors can bestow a machine with more nuanced information about the environment, thereby greatly expanding its range of safe mobility options. Alternatively, a smaller cable can allow a greater number of complementary features to coexist with a camera. The relative resilience of smaller cables against shear fatigue also makes them preferable for connecting to moving or segmented parts.
Furthermore, serialized data transmission requires very little retraining to implement in current manufacturing lines, serialization technology can be easily integrated into testing infrastructure, and under most circumstances repairs and maintenance will likely be either unaffected or made easier. Not only does the technology exist to pave the way for numerous innovations in the automotive and robotics industries, but the skillsets required to utilize this technology at all levels, from design to assembly to troubleshooting, are familiar enough that for many companies, finding qualified personnel would be a non-issue.
As highlighted throughout this paper, the technology of camera data serialization is a deceptively simple, borderline mundane solution to a common, mundane physical problem. The advantages of this humble tool have the potential to allow existing designs to be made more resilient and easier to repair with minimal alteration, while also raising the ceilings of ambitious new design frontiers that have hitherto been theoretically possible but physically impractical.
More powerful computers and sophisticated software are learning to interpret visual data in more nuanced and intelligent ways, but they cannot reach their full potential without receiving external outputs worth interpreting. An essential feature of any intelligent machine is the ability to gather data about its surroundings, and data serialization is an innovation with the potential to pave the way for machines to see more, and do more with what they see.